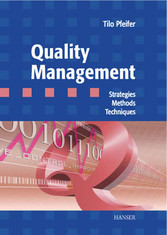
Quality Management
von: Tilo Pfeifer
Carl Hanser Fachbuchverlag, 2002
ISBN: 9783446224025
Sprache: Englisch
620 Seiten, Download: 9461 KB
Format: PDF, auch als Online-Lesen
Preface to the 1 st English-language Edition | 6 | ||
Preface to the 3 German-language Edition | 8 | ||
Content | 10 | ||
List of Abbreviations | 20 | ||
1 Introduction | 24 | ||
References | 32 | ||
Holistic Quality Management | 34 | ||
2 Total Quality Management | 36 | ||
Content | 36 | ||
2.1 Introduction | 37 | ||
2.2 The term Total Quality Management | 38 | ||
2.3 Aspects of Total Quality Management | 39 | ||
2.3.1 Company policy, strategy and objectives | 39 | ||
2.3.2 Leadership | 41 | ||
2.3.3 People orientation and satisfaction | 43 | ||
2.3.4 Process orientation | 44 | ||
2.3.5 Customer orientation and satisfaction | 45 | ||
2.3.6 Result orientation | 47 | ||
2.4 Implementing Total Quality Management | 49 | ||
2.4.1 General approach | 49 | ||
2.4.2 Human Resources | 50 | ||
2.4.3 Quality programs and initiatives | 52 | ||
2.4.4 Performance assessment and TQM maturity | 54 | ||
2.5 Quality awards | 54 | ||
2.5.1 Deming Prize | 56 | ||
2.5.2 Malcolm Baldrige National Quality Award | 57 | ||
2.5.3 European Quality Award | 58 | ||
2.5.4 Ludwig- Erhard- Prize | 61 | ||
2.6 Quality programs, initiatives and tools | 61 | ||
2.6.1 Zero-defects program | 61 | ||
2.6.2 Six Sigma | 63 | ||
2.6.3 Continuous improvement | 65 | ||
2.6.4 Tools used in quality management | 70 | ||
2.7 Summary | 74 | ||
References | 74 | ||
3 Quality Management Systems | 78 | ||
Content | 78 | ||
3.1 Introduction | 80 | ||
3.2 Fundamentals of quality management systems | 81 | ||
3.3 Process-oriented quality management | 86 | ||
3.4 Quality management and standards | 99 | ||
3.5 Introducing QM systems | 105 | ||
3.6 Documenting QM systems | 124 | ||
3.7 Auditing and certification | 135 | ||
3.8 Integrated management systems | 143 | ||
3.9 Summary | 155 | ||
References | 155 | ||
4 Quality and Information | 160 | ||
Content | 160 | ||
4.1 Introduction | 161 | ||
4.2 Knowledge management | 161 | ||
4.3 Quality control loop and quality data base | 173 | ||
4.4 Computer assistance in quality management | 193 | ||
4.5 Overall summary | 209 | ||
References | 209 | ||
5 Quality and Economic Efficiency | 214 | ||
5.1 Introduction | 215 | ||
5.2 Definitions of quality-based costs | 215 | ||
5.3 Types of quality cost accounting | 218 | ||
5.4 Quality-based costs as part of the accounting | 224 | ||
system | 224 | ||
5.5 Objectives and functions of examinations | 228 | ||
of quality-based costs | 228 | ||
5.6 Evaluating quality-based costs | 229 | ||
5.7 Value analysis | 237 | ||
5.8 Target Costing | 242 | ||
5.9 Summary | 244 | ||
References | 245 | ||
6 Quality and the Law | 248 | ||
6.1 Introduction | 250 | ||
6.1.1 Consequences of insufficient quality | 250 | ||
6.1.2 Liability under civil law, | 250 | ||
not responsibility under criminal law | 250 | ||
6.1.3 Liability only for original defects | 252 | ||
6.1.4 Fault and deficiency | 252 | ||
6.1.5 The case of the thrust strut | 253 | ||
6.2 Contractual liability | 255 | ||
6.2.1 Introduction | 255 | ||
6.2.2 Liability for breach of warranty | 255 | ||
6.2.3 Contractual liability for consequential damage | 257 | ||
(“Liability due to positive breach of contract”) | 257 | ||
6.2.4 Guarantee | 258 | ||
6.2.5 Claim to damages from a liable person | 259 | ||
6.2.6 Quality Assurance Agreement | 259 | ||
6.3 Non- contractual liability – meaning and intention | 263 | ||
6.4 Liability under the terms of the German Product Liability Act (ProdHaftG) | 263 | ||
6.4.1 Introduction | 263 | ||
6.4.2 Requirements for liability | 264 | ||
6.4.3 “ Products” and “ Putting into circulation” | 264 | ||
6.4.4 “ Product Faults” | 265 | ||
6.4.5 The damage to be compensated | 266 | ||
6.4.6 Persons legally deemed liable | 266 | ||
6.4.7 Exemption from liability | 267 | ||
6.4.8 Further important provisions of the German Product | 268 | ||
Liability Act (ProdHaftG) | 268 | ||
6.4.9 Summary | 269 | ||
6.4.10 Outcome in the thrust strut case | 269 | ||
6.5 Liability under the terms of § 823 Par. 1 German Civil Code (BGB) | 271 | ||
6.5.1 Introduction | 271 | ||
6.5.2 Requirements of liability | 272 | ||
6.5.3 Sphere of responsibility of the product manufacturer | 273 | ||
6.5.4 Liability of other persons under the terms of | 275 | ||
§ 823 Par. 1 BGB | 275 | ||
6.5.5 Damage to be compensated | 276 | ||
6.5.6 Limitation | 276 | ||
6.5.7 Summary | 276 | ||
6.5.8 Outcome in the thrust strut case | 276 | ||
6.6 Special liability provisions | 278 | ||
6.7 The relationship between individual principles of liability | 278 | ||
6.8 Obligation to safeguard quality | 280 | ||
6.8.1 Introduction | 280 | ||
6.8.2 Manufacturing or production faults under the terms of | 280 | ||
§ 823 Par. 1 BGB | 280 | ||
6.8.3 Scope and nature of inspection | 281 | ||
6.8.4 Liability of the manufacturer for services rendered by | 283 | ||
externally employed staff (particularly components | 283 | ||
suppliers) in relation to his/her product | 283 | ||
6.9 Burden of proof and collecting evidence | 286 | ||
6.9.1 Introduction | 286 | ||
6.9.2 Distribution of the burden of proof in relation to | 287 | ||
manufacturing faults | 287 | ||
6.9.3 Collecting evidence (Documentation) | 289 | ||
6.10 Protection of the manufacturer | 291 | ||
6.10.1 Introduction | 291 | ||
6.10.2 Safety-oriented product and manufacturing | 291 | ||
process design | 291 | ||
6.10.3 Contractual limitation of or exemption from | 292 | ||
liability risks | 292 | ||
6.10.4 Insuring manufacturing risk | 293 | ||
6.11 Statutory and other product safety standards | 294 | ||
6.11.1 Introduction | 294 | ||
6.11.2 Safety standards regulated by law and | 294 | ||
statutory regulations | 294 | ||
6.11.3 Other standards relating to product safety – | 300 | ||
DIN, VDE, ISO and other standards | 300 | ||
References | 304 | ||
Further reading | 304 | ||
Part B Quality Management in the Product Life Cycle | 306 | ||
7 The Early Phases of Quality Management | 308 | ||
7.1 Introduction | 310 | ||
7.2 Planning product characteristics | 311 | ||
7.2.1 Identifying customer requirements | 317 | ||
7.2.2 Planning technical specifications | 324 | ||
7.3 Planning the conditions for realization | 327 | ||
7.4 Quality management in virtual product and process verification, as exemplified by assembly planning | 328 | ||
7.4.1 Basis for virtual product and process support | 329 | ||
7.4.2 Computer-assisted methods of virtual product and process support | 331 | ||
7.4.3 Conclusion | 334 | ||
7.5 QM program planning | 335 | ||
7.6 QFD – Quality Function Deployment | 336 | ||
7.6.1 What is Quality Function Deployment? | 337 | ||
7.6.2 QFD Tools ( House of Quality) | 337 | ||
7.6.3 QFD in practice | 342 | ||
7.7 Rapid Quality Deployment | 344 | ||
7.7.1 Rapid Quality Deployment – The Aachen Model | 344 | ||
7.7.2 Summary | 350 | ||
7.8 TRIZ – Developing innovative products and processes | 350 | ||
7.8.1 Introduction to TRIZ | 352 | ||
7.8.2 Options for integration into Quality Engineering | 354 | ||
7.8.3 Application of the TRIZ method | 354 | ||
7.9 Design Review | 361 | ||
7.9.1 Definition of Design Review | 361 | ||
7.9.2 Types of Design Reviews | 362 | ||
7.9.3 Functions, objectives and execution | 363 | ||
7.10 Quality Evaluation (QE) | 367 | ||
7.11 Fault-Tree Analysis and related methods | 369 | ||
7.11.1 Structure of Fault-Tree Analysis | 370 | ||
7.11.2 The role of systems analysis as the basis for Fault-Tree Analysis | 371 | ||
7.11.3 Drawing up a fault tree | 373 | ||
7.11.4 Evaluating fault trees | 374 | ||
7.12 Design of Experiments (DoE) | 376 | ||
7.12.1 Approach to planning, conducting and evaluating experiments | 377 | ||
7.12.2 One-factor-at-a-time method | 380 | ||
7.12.3 Full factorial designs | 381 | ||
7.12.4 Fractional factorial designs | 391 | ||
7.12.5 Response surface designs | 400 | ||
7.12.6 Robustness | 404 | ||
7.12.7 Methods developed by Taguchi | 406 | ||
7.12.8 Methods developed by Shainin | 407 | ||
7.12.9 Optimal design theory | 411 | ||
7.12.10 Heuristic screening | 412 | ||
7.13 Failure Modes and Effects Analysis (FMEA) | 414 | ||
7.13.1 History of FMEA | 415 | ||
7.13.2 Types of FMEA | 416 | ||
7.13.3 Description of the method | 417 | ||
7.13.4 FMEA as teamwork | 423 | ||
7.13.5 Introducing the method into the company | 424 | ||
7.13.6 Benefits of FMEA | 424 | ||
7.13.7 Computer-assisted tools | 426 | ||
7.14 Statistical tolerancing | 429 | ||
7.14.1 Functions of statistical tolerancing | 429 | ||
7.14.2 Statistical tolerancing methods | 430 | ||
7.14.3 Example of a statistical tolerance calculation for individual dimensions with rectangular distribution | 432 | ||
7.14.4 Example of a statistical tolerance calculation for individual dimensions with normal distribution | 436 | ||
7.14.5 Cost Tolerance Sensitivity Analysis (CTSA) | 437 | ||
7.15 Inspection and test planning | 442 | ||
7.15.1 Functions of inspection and test planning | 442 | ||
7.15.2 Integration of test and inspection planning into the company | 445 | ||
7.15.3 Information flow in drawing up test and inspection plans | 447 | ||
7.15.4 Structure and contents of the test plan | 448 | ||
7.15.5 Procedure for drawing up test plans | 448 | ||
7.15.6 Test and inspection planning as a CAQ module | 457 | ||
7.16 Summary and outlook | 460 | ||
References | 460 | ||
8 Quality Management in Procurement | 470 | ||
8.1 Introduction | 471 | ||
8.2 Procurement strategies | 471 | ||
8.3 Aspects of civil law | 478 | ||
8.4 Functions of quality management in procurement | 480 | ||
8.5 Quality Chain Management | 498 | ||
8.6 TQM in procurement | 501 | ||
8.7 Summary | 503 | ||
References | 504 | ||
9 Quality Management in Manufacturing | 506 | ||
Content | 506 | ||
9.1 Introduction | 507 | ||
9.2 Standards and guidelines | 507 | ||
9.3 Test-data acquisition | 509 | ||
9.3.1 Testing modes and methods | 510 | ||
9.3.2 Measurement and testing engineering | 514 | ||
9.3.3 Computer-assisted test-data acquisition | 521 | ||
9.4 Test-data evaluation | 521 | ||
9.4.1 Preparation, condensing and presentation of test data | 523 | ||
9.4.2 Indicators and indicator systems in test-data evaluation | 528 | ||
9.4.3 Use of test-data evaluation in companies | 529 | ||
9.4.4 Possible uses for the results of the test-data evaluation in the company | 530 | ||
9.4.5 Examples of the use of test-data evaluation | 532 | ||
9.5 Statistical Process Control | 535 | ||
9.5.1 Statistical process behavior | 536 | ||
9.5.2 Application of Statistical Process Control | 539 | ||
9.5.3 Boundary conditions for the use of Statistical Process Control | 543 | ||
9.6 Capability analyses | 551 | ||
9.6.1 Stability and capability of a process | 551 | ||
9.6.2 Defining machine and process capability | 553 | ||
9.6.3 Capability analysis – procedure and principles of calculation | 553 | ||
9.7 Management of inspection and test equipment | 554 | ||
9.7.1 Planning and procuring test instruments | 558 | ||
9.7.2 Administering test and inspection equipment | 560 | ||
9.7.3 Monitoring test equipment | 567 | ||
9.8 Summary | 575 | ||
References | 575 | ||
10 Quality Management in Field Data Evaluation | 580 | ||
Content | 580 | ||
10.1 Introduction | 581 | ||
10.2 Market research | 583 | ||
10.2.1 Surveys | 583 | ||
10.2.2 Observation | 584 | ||
10.2.3 Experiments | 585 | ||
10.3 Serial trials | 585 | ||
10.3.1 Simulation of individual types of loads | 586 | ||
10.3.2 Simulation of the environment | 586 | ||
10.3.3 Field tests | 586 | ||
10.4 Acquisition and processing of field data | 586 | ||
10.4.1 Sources of data | 587 | ||
10.4.2 Data acquisition | 589 | ||
10.4.3 Processing of field data | 590 | ||
10.5 Weibull analysis | 594 | ||
10.5.1 The Weibull distribution function | 595 | ||
10.5.2 The life span grid | 596 | ||
10.5.3 Determining the parameters of the | 598 | ||
Weibull distribution | 598 | ||
10.5.4 Taking account of units which have not become | 600 | ||
defective | 600 | ||
10.5.5 Taking account of other life span characteristics | 600 | ||
10.5.6 Correlation between test and field results | 601 | ||
10.5.7 Failure mechanisms in the Weibull analysis | 602 | ||
10.6 Isochronous diagram | 606 | ||
10.7 Service quality | 607 | ||
10.7.1 Service creation | 608 | ||
10.7.2 Service engineering | 608 | ||
10.7.3 Service management | 608 | ||
10.8 Summary | 610 | ||
References | 610 | ||
Index | 614 |